
our
team
the CAJ team
We are incredibly proud of our CAJ Team, who work tirelessly to produce market leading apples for the world and New Zealand. The team is split into two areas, the Orchard Management Team and the Packhouse Management Team.
The Orchard Management Team
We employ six Orchard Managers, who have collectively over 150 years’ experience with CAJ and apple growing! Although managed in the same way, each orchard has its own nuances in regard to micro-climates and soil types.
Each Orchard Manager is responsible for getting the best crop return from the orchard, and meeting orchard market compliance requirements.
Orchard activities involve pruning, thinning, frost fighting, orchard maintenance, pest control including spraying, employee management, new plantings, soil and water management and harvest. All activities are conducted at the highest possible standards to ensure a successful harvest.
Meet the Orchard Team

PETE VERNON
Field Operations Manager
Pete Vernon is an experienced orchardist and Ettrick local with a vast knowledge of the apple growing industry both locally and nationally. This expertise is put to good use for CAJ in his capacity as Field Operations Manager.
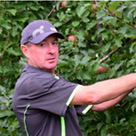
JOHN MCKINNEL
Dumbarton Orchard Manager
John has worked at CAJ for 31 years. He takes satisfaction in growing lots of good quality fruit. And enjoys meeting and getting to know staff and passing on horticultural knowledge.
Away from work, he enjoys family time, including golf, rugby, tramping, multisport and outdoor adventures.

STEVIE LILO
Elderslea Orchard Manager
Stevie has worked on one of our other orchards for many years and has recently taken over as Manager of Elderslea Orchard.
Stevie is well organised and enjoying his new role.

DARRYL PEIRCE
Nithdale Orchard Manager
Darryl is a local identity known for his market gardening enterprise selling pumpkins. Everyone who drives through the valley has stopped for his 3 for $10 pumpkin deal. He is also an experienced orchardist - and rest assured - he is not going to stop the pumpkins any time soon.
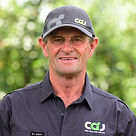
MURRAY BOOTH
Hollandia & Earnscleugh Orchard Manager
Murray is a born and bred Central Otago man and has worked in the horticultural industry since leaving school. Murray has worked for us for 20 years. He enjoys fitness and working outdoors accompanied by his loyal pooch.
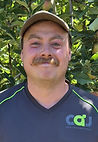
STORM PINN
Hollandia Orchard Manager
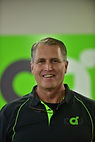
MARK BINGHAM
SI Labour Supply Manager
.
orchards
CAJ has seven beautiful apple orchards spread across Central Otago. We have job opportunities at each of these orchards from 20th November through to end of August.
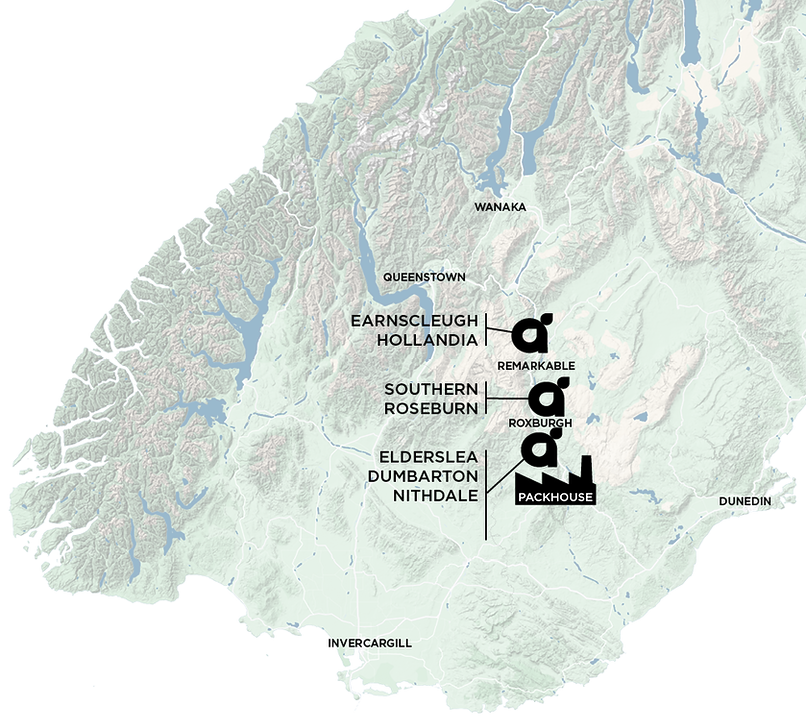
Meet the Packhouse Team

Jackie van der Voort
Jackie is one of the daughters of Con and Eileen van der Voort and has grown up in the horticultural industry. Jackie is now the Post-Harvest Manager and is responsible for the fruit once it has been harvested, until it reaches our customers.

Toni Birtles
Toni is one of the daughters of Con and Eileen van der Voort and is the Finance & Administration Manager. She has been working in the business since 1990 and has seen a lot of changes over the years. She enjoys seeing new people coming into the area every season and her responsibilities include payroll, employment, general administration and finance.
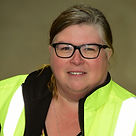
Carla O’Connor
Carla joined the business in 2019 and has over 20 years in the food industry with experience in both Health and Food Safety. Carla is responsible for making sure the business meets all its compliance requirements. Carla is originally from Canterbury and now spends her time between the Teviot Valley and Southland.
packhouse
The state-of-the-art CAJ Packhouse operates for 3-4 months (March to end of July) each year packing apples from all over Central Otago. The Packhouse is designed to pack approximately 2500 TCE’s (boxes) an hour. Each box contains on average 18kg of apples.
The process starts when the Packhouse “calls up” or orders apples from the T&G coolstore, which is just down the road in Ettrick, where the apples are stored from the orchard before packing. They are delivered by truck to the CAJ yard, where they are scanned into the system and loaded into the Apple Dump. The apples are gently floated out of the bins into the apple wash system. The bins are then returned to the orchard for reuse.
Each apple is washed and sanitised by a new in-feed system by Dutch company Greefa, integrated with the CR automation high pressure apple wash system and brush bed. This is state-of-the-art equipment designed and developed in New Zealand.
The clean apples then enter the Packhouse on the 14 Lane Greefa Geosort machine, which has the capability to produce 2500 cartons per hour. This has allowed the team an increase of 60% production since its arrival.
We are using the latest Quality System from Greefa, which allows us to distinguish between different defects on every single apple as it moves through the machine. This is called the defect sorter.
Once an apple has been photographed for defects, it is then weighed by the sizer and then sent to the required packing outlet or what we call, lane. This is where the automation ends, and apples are inspected and placed on the trays and boxed gently by hand.
The finished box then travels on a conveyor down to where it is weighed. Greefa have integrated with Hayden & Custance (H&C), a New Zealand company fabricating and installing world class equipment, for an empty and full box carton system.
The weighed box then proceeds to box closing where an insert is placed in the box and the box is glued closed. From this point the box is scanned and delivered by conveyor to the palletisation area, where the boxes are palletised, strapped and labelled before final sign off and release for pickup and delivery to our customer.
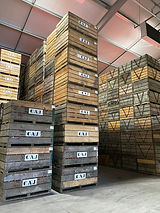
Our Partners
We work closely with Turners and Growers (T&G) who help us execute the smoothest supply chain from tree to sea. T&G are industry leaders in refrigerated produce transport and packaging, and are growing to become New Zealand’s first choice in transportation.
They have 9 depots nationwide and we utilise their coolstores in Ettrick and in Dunedin. We use the Ettrick coolstore to store our apples in optimum conditions for quality retention after harvest and before they need to be packaged up into boxes and shipped.
Once packaged up in boxes in our Packhouse, the boxes are transported to Dunedin where they are stored in the T&G coolstore there before being transported to Port Chalmers and onto a container ship to take them across the world to our many markets.
CAJ is also part owner with Sid Birtles of the Remarkable Orchards. The Remarkable Orchards are mixed fruit orchards growing both stone and pip fruit located in East Roxburgh. They have summer fruit job opportunities for keen people and opportunities outside the CAJ seasonal work. Find out more here www.remarkableorchards.co.nz